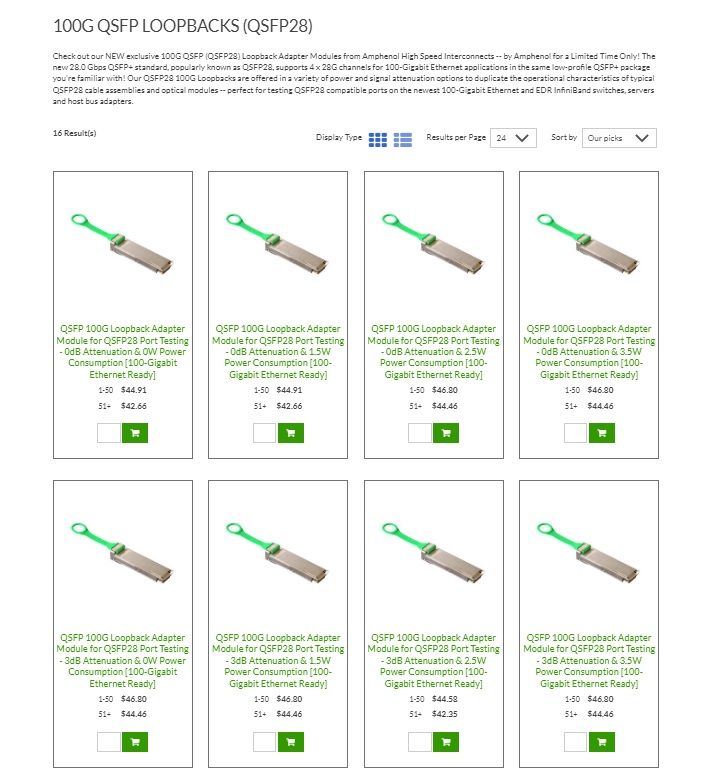
Choices…Which One is Correct? They All Look The Same! Cable Guy, Please Help!
(Pictured: Half of the SIXTEEN Possible QSFP28 Loopback Transceiver Modules Available)
Upon joining the Amphenol Cables on Demand team in 2007 as Product Manager, shortly after the company’s launch, it didn’t take long to realize that despite having just worked in the same interconnect manufacturing industry for nearly three years (albeit on the defense/aerospace side for a competing firm), I still had a sizeable amount of studying to do in order to be up-to-speed. The interconnect industry in particular can be intimidating for a newcomer, as there is not only a plethora of industry-specific lingo you need to know in order to speak “the language”, but you also need to have a comfortable background knowledge of the application-specific implementation of the cable and connector products on offer as they are integrated into any number of real-world network and communications platforms.
Needless to say, it’s a lot to take in. I can only imagine the difficulty it would present to someone on the procurement side who have only just recently entered the industry and are immediately confronted with a scenario such as this one:
A member of your company’s Engineering or IT staff have just shot you an e-mail asking you to order a few dozen “QSFP Loopbacks” to have on-hand so that they can readily test the ports on the 48 new server racks they’re installing in the company’s newly-expanded datacenter. You type “QSFP Loopbacks” into Google and have just been directed here to the Amphenol Cables on Demand website, where you land on our QSFP+/QSFP28 LOOPBACK MODULES product category page, as pictured below:
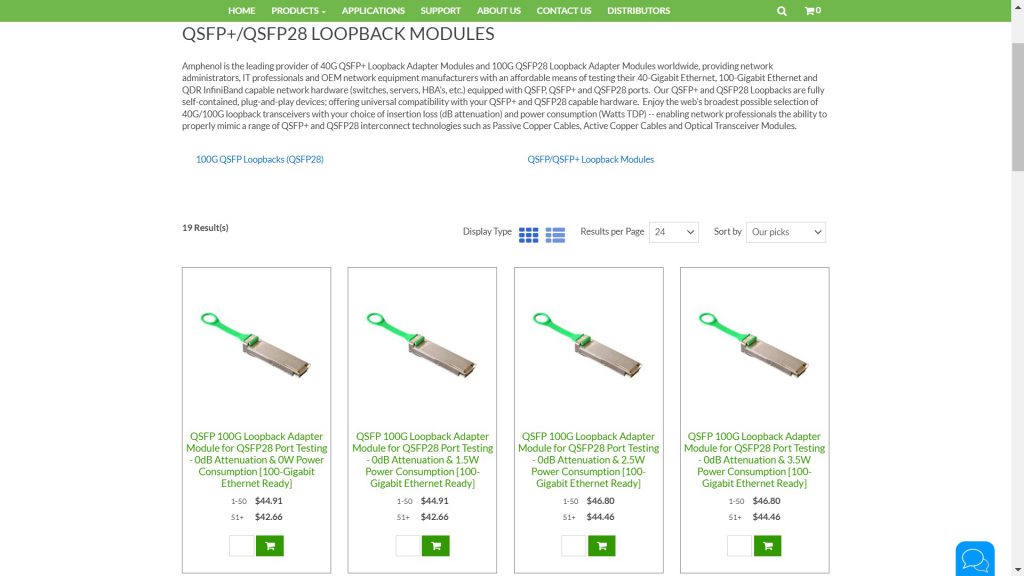
Assuming your IT Department is unable to provide you with any additional guidance, or the details they’ve offered is a bit too ambiguous to work with, you have to make a prompt decision: Do I click on the category link titled, “100G QSFP Loopbacks (QSFP28)“? Or do I click on the category link that’s listed as “QSFP/QSFP+ Loopback Modules“? In a situation such as this, the safest bet is always going to be the first option, 100G QSFP Loopbacks (QSFP28). Why choose the 100G QSFP28 option? The answer comes down to two simple, yet critical, words — REVERSE COMPATIBILITY.
What is Reverse Compatibility? Reverse Compatibility is a term that frequently arises within the IT/Datacenter market, specifically as it relates to cable and connector products used in Ethernet-based networking applications. Ethernet is of-course the most prominent computer networking protocol / signaling method in use today. Ethernet was initially conceived as part of a DARPA defense research initiative at the height of the Cold War, where they needed a mission-critical and reliable method of transmitting essential data that they split up into smaller digital “packets” that were coded and ordered in such a way that they could then be re-assembled into uniform data on the other end.
This packet-based communications protocol was the ideal solution as it solved two key problems. First, smaller packets of data could successfully be sent over less-than-ideal transmission mediums, such as overhead power lines or traditional phone lines, where bandwidth is naturally restricted. Second, by using packets alongside a form of bi-directional error checking, if a nuclear missile were to have knocked down a particular set of phone or power lines in a city, the lost packets could then be requested and re-sent via an alternate route. This day-in-age, we don’t think of Ethernet in these terms, but it was this core design consideration that also led to the key feature of Reverse Compatibility. As the technology surrounding Ethernet evolved, you still wanted (or needed) older Ethernet equipment to work alongside of newer Ethernet equipment, with the ultimate objective being the successful transmission of essential digital information over a vast network of disparate telecom hardware.
The QSFP interface, which stands for Quad Small Form Factor Pluggable, is a constantly evolving external I/O (Input/Output) interconnect platform designed for use on Ethernet-based High-Speed Networking equipment such as Multi-port Network Switches, Server Racks, Network Attached Storage Devices, Host-Bus Adapters (HBAs), Passive Copper Cables, Active Copper Cables, Active Optical Cables (AOCs), Optical Transceiver Modules and finally, what we are discussing today, Loopback Adapter Modules/Transceivers. QSFP was always designed to be an evolving standard that had Reverse Compatibility as one of its core features, thereby enabling increases is speed/bandwidth with time whilst ensuring broad compatibility with older hardware within the network.
This concept may seem familiar as it is the core tenet of another Ethernet-based I/O standard — Ethernet Over Twisted Pair. Ethernet Over Twisted Pair is the single-most prevalent networking transmission medium in use today as it represents the most cost-effective and reliable means of routing Local Area Networking (LAN) traffic within residential homes, small offices, larger commercial buildings and factories. Twenty-Plus years ago, Ethernet traffic was primarily running 10/100, a mixture of 10-Megabits-per-second and 100-Megabits-per-second devices connected via Category-5 (CAT5) Unshielded Twisted Pair (UTP) wiring. CAT5 wire featured 4 twisted pair wire bundles within its PVC cable jacket, but only utilized 2 of those pairs. The additional two un-used pairs were specifically included within the standard as a means to allow the networks to evolve technologically and still use the same CAT5 cable that was installed throughout the building envelope.
The next big evolutionary step in Ethernet technology was the advancement from 10/100 Fast Ethernet to the vastly superior 1000BASE-T Gigabit Ethernet technology standard. It offered 10x faster networking speeds than the old 10/100 standard, while maintaining compatibility with existing CAT5 wire. To support Gigabit Ethernet, they had to make use of those two un-used wiring pairs within the CAT5 cable. They also added a more advanced equalization circuit to reduce line noise and increase bandwidth. However, CAT5 couldn’t reliably support Gigabit Ethernet transmission over particularly long distances. This led to the development of the more familiar Category-5e (CAT5e) cabling standard that is still found in many building networks today.
CAT5e utilized a higher rate of wire twists-per-inch of cable. The higher the twist rate-per-inch, the better the cable was at rejecting noise/cross-talk. To further prevent a form of cross-talk called Near-End Cross-talk (NEXT), in which noise from one pair could leach into the adjacent pair within the same cable, every pair used a different twist-per-inch rate. This design lent itself to superior 1000BASE-T Gigabit Ethernet performance, supporting Gigabit transmission at distances up to 100-meters (330-feet) in total. Amphenol Cables on Demand stocks a sizeable variety of Category-5e (CAT5e) Cables in multiple color, length, crossover and shielding configurations to suit any type of installation.
The design committee responsible for drafting the CAT5e cable standard knew that as designed, the CAT5e wiring system had essentially maximized its design capacity, requiring a major systemic evolution whilst maintaining backwards compatibility with prior Ethernet standards. This led to the development of the popular Category 6 (CAT6) cabling standard. CAT6, out of all of the networking patch cord types on offer here at Cables on Demand, is by far the most popular and best-selling Ethernet cable currently offered. It also represents the most widely deployed Ethernet cable type presently in-use worldwide. CAT6 was a sufficient enough evolution over CAT5e that it enabled the first cable of the series to support a massive 10-times boost in supported speed to 10-Gigabits-per-second via the 10GBASE-T (10-Gigabit Ethernet) communications standard utilizing the same 4-pair wiring scheme as CAT5e.
CAT6 cabling is capable of supporting 10GBASE-T 10-Gigabit Ethernet traffic at lengths up to about 35-meters, or a little over 100-feet. The capability to perform at such a massive speed increase over its predecessor is due to two design considerations. First, a thicker wire AWG was typically utilized, thereby reducing systemic signal loss (attenuation) and better able to handle the extreme bandwidth requirements (over 250 MHz) demanded by 10-Gigabit Ethernet. Second, it introduced what is known as a “star-filler” or X-shaped cable spline which runs down the entire length of the wire. Its job is to physically separate the internal wire pairs, thereby preventing accidental signal coupling and induced cross-talk, which is a major threat to stable signal distribution at high-speeds.
However, this self-limiting design that prevents signal transmission beyond that 35-meter or 100-feet distance threshold is by no means a minor issue. It is a major hinderance, as it is often impractical or impossible to keep Ethernet-based networking design decisions within that short distance window. This demanded the use of fiber optic based optical transceiver modules or Active Optical Cables (AOCs) for any runs beyond that 35m/100ft limitation, which increases the cost by up to 50-times or more versus the cost of being able to just use CAT5e or CAT6 cable instead. The cost burden here is so substantial that it could make or break many IT budgets.
Fortunately, the technology evolved just-in-time with the introduction of the newest widely-implemented twisted-pair-based wiring platform, Category-6a, also known as Category-6 Augmented. As to why they didn’t just call it CAT6e instead, for CAT6 Enhanced is unclear. Perhaps it was simply to avoid confusing the two standards of CAT5e with a potential CAT6e. Amphenol Cables on Demand stocks a substantial inventory of CAT6a Network Patch Cords in a variety of lengths and colors to meet nearly any installation scenario. What is CAT6a’s big evolutionary leap over its CAT6 predecessor? It supports full 10GBASE-T 10-Gigabit Ethernet-based network throughput over its entire length limit, up to 100-meters or 330-feet. This substantial distance improvement is a game-changer, as it now makes almost all intra-building connection distances possible using affordable CAT6a cabling.
The big technological leap that enables CAT6a to perform so reliably at 10.0 Gigabits per second is its use of full concentric aluminum mylar foil shielding across the entire cable length, along with appropriately shielded RJ45 connectors, all terminated to a drain-wire that traverses the whole wire run. This sufficiently suppresses the dreaded problem with Alien or Far-End Cross-Talk that is the predominant problem that impedes 10-Gigabit signal transmission. The shielding mechanism also adds an additional benefit for networks utilizing PoE (Power over Ethernet). The natural thermal heat build-up of handling up to 90-watts of power over long distances of wire that is less-than-ideal for handling high-current power can quickly become problematic, especially in common installation scenarios in which many cables are bundled together and routed through conduit. The aluminum shielding allows this heat to better radiate evenly into the surrounding atmosphere, rather than creating potential “hot pockets” (and I don’t mean the delicious microwavable lunch-time snacks) that reduce system efficiency and pose a potential fire hazard.
This transitions nicely to a relevant issue — Heat. The major systemic evolution of Ethernet over twisted pair from a lowly 10-Megabits-per-second to a staggering 10-Gigabits-per-second doesn’t come free. There is an inherent penalty. The reason-being, these aforementioned design improvements to the wire designs alone are not enough to make the system work. There is a lot going on behind the scenes on the equipment side, both on the transmitting and receiving ends, that enables the successful transmission of 10.0-Gbps signals over 4 relatively cheap pairs of wire in a typical CAT6a cable. Massive amounts of signal processing, equalization, pre-emphasis, de-emphasis, amplification, error correction, phase correction and zero offset algorithms have to run near continuously and in conjunction with each-other just to make the system work as it should.
This aforementioned processing requirement creates a significant power and thermal burden that the system designers have to contend with. When you have a typical 24 or 48 port network switch that crams all of those ports into a narrow 19-inch wide by 2 or 3-inch tall server switch, a switch that then ends up stacked 20-switches tall on a rack that is adjacent to the same dense stack of equipment, you end up only compounding the problem further. The power and air conditioning requirements for a typical datacenter are so vast that many companies have specifically located their datacenters sometimes thousands of miles away from their base-of-operations just so that they can operate in cooler climates, locations with cheap hydroelectric power, or a combination of both.
As a consequence, network switches will seldom operate with a majority of their backbone communications ports running via 10GBASE-T 10-Gigabit Ethernet over Twisted Pair wiring. The power demand is literally 10-times higher or worse and the thermal heat build-up is so extreme that an alternative design methodology was needed. The solution?
The Quad Small Form Factor Pluggable (QSFP) connection standard for 10-Gigabits-per-second or higher data traffic resolves the aforementioned problems and represents the most widely implemented I/O system for high-performance network back-bone communications. In this layout, all of the heavy lifting is done via the QSFP style connections, or its smaller SFP counterparts, relegating the switch RJ45 ports with handling just 1-Gigabit Ethernet data transmission from the switch level to the individual computer level within the network. This saves power and reduces heat. While the cost of QSFP-based cabling is certainly higher than your typical CAT5e, CAT6 or CAT6a cable, the long-term power savings and improved thermal management of the network more than makes up for the cost disadvantages.
To test a port on a server switch prior to fully deploying the network with an actual cable run, IT professionals make use of what’s known as a Loopback Adapter. Its core function is exactly what it sounds like. A port on a switch supports bi-directional signal transfer natively, that is, it handles data transmission and data reception at the exact same time, both operating at full speed. This enables the user to test the functionality of each port by simply “looping back” or shorting a connection between the send and receive pathways of the particular port. In the old days, loopback testing could be done on the cheap on 10/100 Ethernet based systems. All you had to do was build a crossover cable, which basically was a regular looking CAT5 patch cord that had the send pairs loopback into the receive pairs.
This cheap and easy method of testing with a homemade loopback crossover cable is no longer feasible at higher data rates, especially when it comes to the use of a QSFP-style interface as the means of terminating your own QSFP cable in the field doesn’t exist due to the complexities of the cable assemblies. This is what QSFP Loopback Modules were designed for specifically. They internally route the send and receive signal traces in a loopback arrangement so that you have a compact and convenient connector module that can be quickly installed on a switch, used for testing it, only to be removed and stored in the IT department’s bag of tools where they can use it later to test another switch on an as-needed basis. Each switch features its own internal set of command line tools that IT staff can utilize to check a port’s data transmission rate, packet losses, and the power consumed in doing so.
The most expensive loopback testing method possible for 40-Gigabit Ethernet QSFP+ and 100-Gigabit Ethernet QSFP28 based ports is to purchase an expensive QSFP+ or QSFP28 Optical Transceiver Module and install an MTP/MPO fiber optic loopback adapter cable in the module’s MTP/MPO optical I/O chain. While this works, it is needlessly complex, overly expensive and doesn’t fully capture all of the possible installation scenarios that one of our QSFP+ or QSFP28 Loopback Adapter Modules can mimic. That is the core reason behind our offering so many different configurations of loopbacks. Each one is designed/configured in such a way as to mimic as precisely as possible an equivalent real-world cable installation, using a specific cable type AND cable length.
The fact is, the QSFP style interface offers IT professionals with a myriad of cable options to choose from as it relates to connecting the QSFP+ or QSFP28 port on one switch with the QSFP+ or QSFP28 port on another switch or device. These options include any of the following:
Option #1: 40-Gigabit Ethernet QSFP+ Passive Copper Cable in lengths from 0.5m to 8m
Option #2: 40-Gigabit Ethernet QSFP+ Active Copper Cable in lengths from 0.5m to 20m
Option #3: 100-Gigabit Ethernet QSFP28 Passive Copper Cable in lengths from 0.5m to 8m
Option #4: 100-Gigabit Ethernet QSFP28 Active Copper Cable in lengths from 0.5m to 20m
Option #5: 40-Gigabit Ethernet QSFP+ Optical Transceiver Module via Multi-Mode Fiber up to 100m
Option #6: 40-Gigabit Ethernet QSFP+ Optical Transceiver Module via Single Mode Fiber up to 5km
Option #7: 100-Gigabit Ethernet QSFP28 Optical Transceiver Module via Multi-Mode Fiber up to 100m
Option #8: 100-Gigabit Ethernet QSFP28 Optical Transceiver Module via Single Mode Fiber up to 5km
With such a vast array of cabling options at one’s disposal, how do you effectively test out a specific port beforehand to ensure that it will work as expected when the port is connected in real-life via a pre-determined style and length of cable? To do this test correctly, you need to select the QSFP+ or QSFP28 Loopback Adapter Module whose internal specifications are designed to most closely mimic the real-world performance of the cable style and length you plan on deploying. This is a critical consideration. Some switches that are oriented to the lower-end of the market, for instance, may lack the capability of handling a higher power load for any given port, which limits the eventual cabling choices and thus the loopback suited to its testing/emulation would be comparably impacted.
If, however, information is limited and there are a great deal of “unknowns” in the equation, where perhaps the ultimate choice of cable is in-flux and the IT staff merely want the ability to make sure ports work or don’t work, a simple black-or-white decision where these other factors simply are immaterial. If that’s the case, there is one particular High-Speed Loopback Adapter Module available that suits this requirement and would generally be considered as the most “universal” of all the choices. That particular module is shown below. It is Cables on Demand part number, “SF-100GLB0W00-0DB”, as shown below.
Why is this one, in particular, the right choice for a universal QSFP loopback? First, although this is sold as a 100-Gigabit QSFP28 Loopback, it is 100% reverse compatible with older-generation 40-Gigabit Ethernet QSFP+ enabled equipment. When connected to such a system, our loopback adapter will detect that the equipment is data capped at 40-Gigabits per second and will lower its throughput speed to match said equipment. Second, this module features 0dB attenuation and 0-Watts power consumption. This represents the lightest thermal and power load conceivable so that it is guaranteed to work on all QSFP type equipment, including any that may be restrictive in power-handling characteristics. Thus, as it relates to the common customer scenario presented at the start of this blog post, someone tasked with getting “QSFP loopbacks” with very little relevant information at their disposal to further narrow-down their product selection should absolutely choose this product below above all others.
![QSFP 100G Loopback Adapter Module for QSFP28 Port Testing - 0dB Attenuation & 0W Power Consumption [100-Gigabit Ethernet Ready] QSFP 100G Loopback Adapter Module for QSFP28 Port Testing - 0dB Attenuation & 0W Power Consumption [100-Gigabit Ethernet Ready]](https://cablesondemand-2.azureedge.net/img/product/SF-100GLB0W00-0DB_1.jpg?fv=1C990F8DFEAE5537E1A8E11CC6EC2EF0-5471)
1-50 | $44.91 |
51+ | $42.66 |
In Part #2, the closing second chapter of this technical blog series on Loopback Adapter Modules De-Mystified, we will explore how the remaining 15 module design choices come into play, how they precisely align with the multitude of cable choices we’ve presented here that loopbacks are configured to emulate, with a particular emphasis on these two essential performance parameters:
Key Parameter #1: Power Consumption (In Watts)
Key Parameter #2: Signal Attenuation (In dB)
It is these key parameters in particular that should help guide your purchasing decision. We shall explore these parameters in far greater depth in our follow-on blog post, which will be available in late May, 2022.
Thank you for reading the first part of our two-part series and we look forward to presenting you with the finale. Its publication will be formally launched and linked with alongside our next newsletter blast.
Sincerely,
The Cable Guy
Amphenol Cables on Demand Product Manager
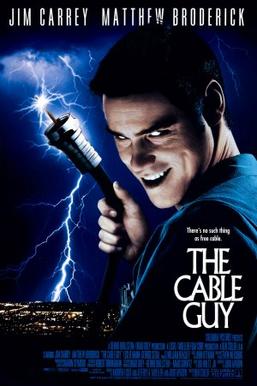
Nick "The Cable Guy" Blas has enjoyed a fulfilling career as Amphenol Cables on Demand's exclusive Product Manager and resident tech expert, having worked for the company just months after its debut launch in December of 2006. Prior to Amphenol, Mr. Blas worked for another interconnect giant, Deutsch Connectors (Now Tyco), in their Defense and Aerospace division as their youngest Program Manager at just 25. While in college for Electrical Engineering and Business Administration/Information Management at UC Riverside and Cal State San Bernardino, Mr. Blas excelled in retail marketing management and sales for Canon USA and Hewlett Packard, both in their printer and imaging business units. Mr. Blas has been a self-professed "tech nerd" since age 10, with a particular fascination with radio and broadcast communications and antenna systems, which led to his college grant work for TRW Corp. Mr. Blas earned his Executive MBA at California State University, Monterey in 2012. He and his wife, Shelly and son, Ethan, currently reside in the stunning Ozark mountains, just outside of Bentonville, Arkansas (home of the world's largest company, Wal-Mart).